Aluminum's strength, corrosion resistance and heat dissipation provide significant advantages for machine designers.Our proprietary thin-walled aluminum technology makes it possible to choose aluminum die-casting for more applications. Due to the fact that the ongoing growth of automobile manufacturing, power systems and battery-electric platforms continues to support an increase in aluminum penetration.
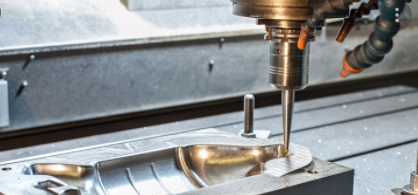
A recent research showed that, by 2026, aluminum, the fastest-growing automotive material, is projected to increase to 514 pounds per vehicle (PPV), up from 12 per cent by 2020. American research and DuckerFrontier consulting firms evaluated the newest materials from North American light vehicles, including automobile manufacturers and suppliers, across the automotive value chain. The use of automobiles, white components and chassis, as well as electric power platforms, and electric battery cars is increasing in the automotive industry because of its traditional vehicles (BEV).
"The use of aluminum in vehicles also rises with increasing customer demand and environmental concerns. This demand is growing, since the strength and light weight of aluminum enables manufacturers to respond to the changes in the automobile industry today. We have been mobile The fast-growing electric vehicle sector is excited about the growth potential of metals "Ganesh Paneer, Chairman of the Transportation Group Aluminum Association said. "The penetration rate for the aluminum market in the automotive industry has increased year after year over the past 50 years and is planned to continue to rise. The growing use of electric vehicles has increased the use of aluminum to increase the range and help balance battery weight and cost. It ensures consumers are able to choose high performance, safe and fun-filled cars and trucks and better preserve the environment."
As the development of multi-material vehicles, automobiles and SUVs advances, car manufacturers will increase the use of aluminum in automobiles. According to the latest DuckerFrontier 2020 research, aluminum contents and prospects in light-duty vehicles in North America still provide important options to replace heavy steel and assist car makers achieve reduction goals.
Doors are the largest rise in net aluminum content per vehicle and the penetration rate will reach 30 per cent by 2026. In addition, the adoption rate of aluminum caps is predicted to reach 81% by 2026, while door panels are projected to reach 44%. The total aluminum content is estimated to reach 570 PPV by 2030, an increase of 24% in the following 10 years.
Growing power generation will increase demand for projects for aluminum die casting and high pressure dietary castings with their increasing usage in battery, engine housing and body structural applications. The major uses for vehicle safety and extrusion (CMS) systems are expected to increase by 10 percent between 2016 and 2022.
"With new features increasing in content and weight, greater safety regulations and a move to electrification, the aluminum industry is expanding and developing solutions that fulfill most of the pressing needs of automakers. Year after year, development halted till 2030 "Abey Abraham, CEO of DuckerFrontier, said.
In the constantly evolving business, automakers continue to choose Aluminum, as shown by the current introduction of cars with substantial use of aluminum housings and structural components. It was an important area of American manufacturing and a healthy American economy because the automobile aluminum industry developed strongly. More than $3 billion was invested and pledged by the aluminum sector to ensure expanded production capacity. As a result of continuous demand growth, the US automobile industry has continued to invest in domestic manufacturing employment since 2013.
Aluminum cars: a win-win partnership
Aluminum and automobiles are two natural partners as they meet the criteria of sustainable products and applications – better than most other materials – and contribute to the development and production of environmentally friendly cars by automakers.
The advantages of this material are well known: when combined with the appropriate components, it is very lightweight and robust. It can be recycled energy-efficiently without any difficulties, thus substantially saving resources. In several methods, casting, rolling, extrusion and forging may be utilized. Aluminum is used as a bumper component for conveyor and clutch housings and body panels.
The addition of aluminum components enables a decrease of around one third of the weight of steel products. About 3,5 liters of gasoline per 1000 kilometers may be saved each time every 100 kilograms and the greenhouse gas CO 2 is reduced by the same amount.
geometry dash subzero is the only winter-themed press-start game in the Geometry Dash series. Enroll right away to start making amazing jumps with seven geometric shapes!